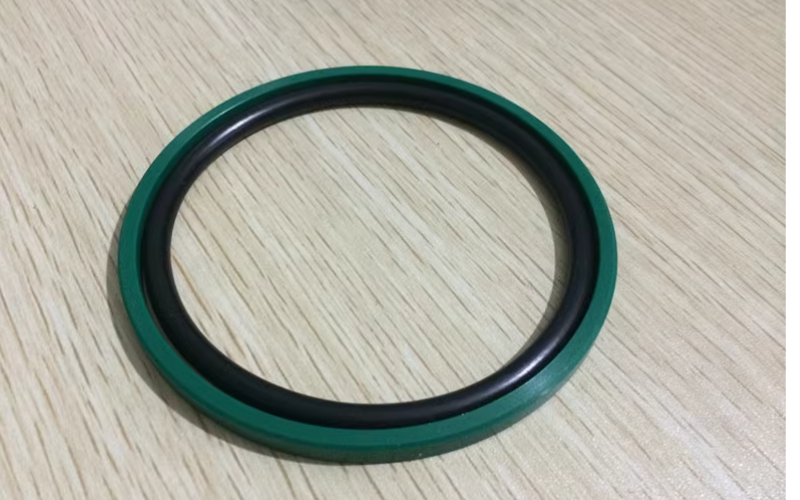
Seals are crucial components in machinery, as they prevent the leakage of fluids between compartments and protect critical parts from contamination. Parker has developed a reputation for producing high-quality seals that offer specific benefits for different applications.
This article explores the application-specific benefits of using Parker seals, highlighting their role in enhancing performance and reliability across various sectors.
Understanding the Role of Seals
Seals are used in mechanical systems to fill gaps and spaces between moving and stationary components, ensuring that liquids, gases, or other contaminants do not pass through. Effective sealing is vital for the operational efficiency and longevity of machinery. Parker’s seals are designed with advanced materials and innovative technologies tailored to meet the unique challenges of each application.
Benefits
- Automotive Industry
In the automotive sector, seals are used in engines, transmissions, and braking systems. Parker seals are designed to withstand the high temperatures and pressures typical in automotive applications. They help enhance vehicle performance by ensuring tight seals that prevent fluid leaks and reduce friction, leading to better fuel efficiency and reduced emissions. For example, Parker’s O-rings and gaskets are made with materials that resist degradation from oil and fuel.
- Aerospace Industry
The aerospace industry requires extremely reliable and durable seals due to the critical nature of its applications. Parker in aerospace are used in hydraulic systems, fuel systems, and engines. These seals must resist extreme temperature fluctuations and exposure to aggressive chemicals. Parker’s aerospace seals are made from materials that can withstand rapid changes in temperature and pressure, ensuring the safety and reliability of aircraft operations.
- Oil and Gas Industry
Seals used in the oil and gas industry face harsh environments, including exposure to corrosive substances and extreme pressures and temperatures. Parker provides robust sealing solutions that can handle these challenging conditions, preventing leaks that could lead to environmental hazards and costly downtime. The durability of Parker helps maintain the integrity of pipelines, valves, and drilling equipment, crucial for efficient and safe extraction and transportation of oil and gas.
- Healthcare and Pharmaceutical Industry
In medical devices and pharmaceutical equipment, seals must meet stringent cleanliness and biocompatibility standards. Parker seals are used in applications such as surgical instruments, fluid delivery systems, and drug dispensing equipment. These seals are made from materials that are not only resistant to various sterilization processes but also compatible with a wide range of medications and bodily fluids, ensuring patient safety and product efficacy.
- Food and Beverage Industry
Seals in the food and beverage industry must prevent contamination and withstand regular cleaning with harsh sanitizers. Parker’s seals for this sector are designed to be non-toxic and resistant to wear and tear from aggressive cleaning agents. They help maintain the hygiene and integrity of food processing and packaging machines, ensuring that products are safe for consumption.
- Manufacturing and Industrial Applications
In general manufacturing, seals are used in a variety of machines and equipment, from hydraulic presses to conveyor belts. Parker seals offer excellent durability and resistance to wear, essential for maintaining the efficiency and longevity of industrial machinery. These seals can be customized to fit a wide range of applications, providing flexibility and reliability in diverse manufacturing settings.
Innovation in Material and Design
Parker’s continuous innovation in material science and design is key to the development of seals that meet the specific needs of different industries. The company uses a variety of materials, including polymers, elastomers, and thermoplastics, which are selected based on the application’s requirements for temperature, pressure, and chemical resistance.
Advantages
- Reliability
Parker’s rigorous testing and quality control ensure that their seals are highly reliable and perform well under expected conditions.
- Customization
Parker offers customized seal designs to meet the specific requirements of various applications, ensuring optimal performance.
- Technical Support
Parker provides exceptional technical support, helping customers select the right seals and troubleshoot any issues.
Conclusion
Parker seals are essential components in numerous industries, providing tailored solutions that enhance the safety, efficiency, and reliability of applications. From the high demands of the aerospace industry to the stringent standards of healthcare, Parker’s expertise in sealing technology delivers significant benefits. As industries continue to evolve, Parker’s ongoing innovation and commitment to quality will remain crucial in meeting the changing needs of its global customers. Thank visiting signatureblogs.com